Füllen, Ausgleichen, Glätten
Zur fachgerechten Herrichtung eines Untergrundes gehört das Ebnen seiner Oberfläche. Je nach Zustand können regelrechte Verfüllungen in Dicken von mehreren Zentimetern erforderlich werden oder es reicht ein Feinausgleich von 1-2 mm. Auch sind Spachtelschichten notwendig, wenn nicht saugfähige Böden vorliegen. In diesen Fällen ist der saugfähige Untergrund erst durch den Einsatz von Ausgleichsmassen in 2- bis 3-mm- Schichten realisierbar.
Grundvoraussetzung für den Einsatz von Spachtelmassen ist ein stabiler Untergrund, der bereits entsprechend mechanisch vorbereitet und grundiert ist.
Hauptaufgaben der Spachtelmassen
Füllen
Für die Verfüllung von Löchern oder zur Anspachtelung von Rampen sind standfeste Spachtelmassen (THOMSITRS 88) vorgesehen. Sie lassen sich in der Konsistenz je nach Wasserzugabe dosieren und erhärten innerhalb kurzer Zeit (ca. 30 – 60 Min.).
Ausgleichen
Häufig ist die Aufgabenstellung so, dass besonders stark zerklüftete, unebene Untergründe oder Böden mit deutlichem Gefälle zu egalisieren sind. Für den großflächigen Einsatz gibt es daher fließende, selbst verlaufende Dickschichtausgleiche wie THOMSIT DS 40.
Glätten
Der häufigste Anwendungsbereich ist jedoch die Glättung eines Untergrundes in Schichten von 1-3 mm. Die Spachtelmassen werden dazu selbstverlaufend eingestellt. Unter anderem diese Eigenschaft sorgt dafür, dass später keine unschönen Abzeichnungen von Unebenheiten im Oberbelag entstehen.
Einteilung der Ausgleichsmassen nach Bindemitteln
Zementgebundene Massen
Sie gehören zu den Standardmassen und haben den Vorteil der zügigen Anmachwasserbindung auch in dickeren Schichten durch den Zement. Es gibt zudem so genannte Schnellspachtelmassen, die beschleunigte Zemente enthalten, so dass die Belegreife besonders zügig erreicht wird (ca. 1-3 Stunden). Je nach Rezepturbestandteile decken diese Massen besondere Einsatzbereiche ab: z. B. Faserzusatz für Holzuntergründe oder hoher Kunststoffanteil für große Belastungen (Gabelstapler, Hubwagen).
Im THOMSIT Sortiment gehören dazu z. B. THOMSIT DX, XXL Power, FA 97, SL 85, XXL Xpress
Gipsbasierte Massen
Gipsspachtelmassen sind vor allem für den Einsatz auf Gipsuntergründen (Calciumsulfat-Estriche, Anhydrit-Estriche) vorgesehen. Aufgrund ihrer besonders geringen Schwindung eigenen sie sich auf nahezu allen Altuntergründen und Trocken-Estrichen. Auch Gipsmassen gibt es mit Faserzusatz für den Einsatz auf Holzuntergründen. In dicken Schichten (> 3 mm) trocknen sie allerdings vergleichsweise langsam (Technische Merkblätter beachten).
Im THOMSIT Sortiment gehören dazu z. B. THOMSIT AS 1, AS 2
Kombi Spachtelmassen
Diese Massen eignen sich auf fast allen Untergründen und zeichnen sich zudem durch rissfreie Ergebnisse aus. Mittels einer speziellen Zusammensetzung von modernen und nachhaltigen Bindemitteln sowie der Verwendung besonderer Additive trocknen diese auch bei ungünstigen klimatischen Bedingungen zuverlässig und eigenen sie sich vor allem bei zeitkritischen Projekten mit schnell benötigter Belegereife.
Im THOMSIT Sortiment gehören dazu z. B. THOMSIT XF 700 Premium-Dickschicht-Ausgleich, XF 500 Premium-Ausgleich und XF 300 Boden-Ausgleich.
Dispersionsspachtelmassen
Spachtelmassen auf Dispersionsbasis sind einsatzfertige Kunststoff-/Füllstoffmischungen, die vorzugsweise auf alten Nutzbelägen als so genannte Migrationssperre (z. B. als „Schutzschicht“ gegen Weichmacherwanderung aus PVC-Altbelägen) zum Einsatz kommen. Sie sind nur in sehr dünnen Schichten bis max. 1 mm in einem Arbeitsgang einsetzbar und sollen in der Regel die Strukturen des jeweiligen Altbelages ausgleichen. Schichten aus Dispersionsspachtelmassen sind nicht saugfähige Untergründe.
Im THOMSIT Sortiment gehört dazu z. B. THOMSIT FF 69 Flex Finish
Reaktionsharzspachtelmassen
2-K-Polyurethanspachtelmassen stellen Spezialprodukte dar, die aufgrund ihrer elastischen Einstellung auf nachgiebigen Untergründen wie Dämmunterlagen oder Sportböden geeignet sind. Darüber hinaus lassen sich Metallböden und bestimmte Asphaltuntergründe ebenso mit diesen wasser- und spannungsfreien Reaktionsharzen überziehen. Schichten aus Reaktionsharzmassen sind nicht saugfähig.
Im THOMSIT Sortiment gehört dazu z. B. THOMSIT S 810.
WICHTIG!
Achtung: Nicht alle Untergründe sind dafür geeignet, in dicken Schichten mit Spachtelmassen überzogen zu werden. Bei Gussasphalten sollten z. B. 5-mm-Schichten nicht überschritten werden, da sonst mit Rissbildung im Estrich gerechnet werden muss. Holen Sie sich in solchen Fällen oder wenn besonders dicke Ausgleichsschichten eingesetzt werden sollen immer erst eine anwendungstechnische Beratung.
Hinweise zur Anwendung von Spachtelmassen
Die Verwendung der jeweiligen Masse ist an bestimmte Bedingungen geknüpft. Ein wichtiges Augenmerk liegt dabei auf den raumklimatischen Verhältnissen. Etwa die Hälfte des Anmachwassers einer Spachtelmasse muss verdunsten, der Rest wird vom Bindemittel, z. B. Zement, chemisch gebunden. Aus diesem Grund ist auf der Baustelle unbedingt dafür zu sorgen, dass einerseits das Überschusswasser aus den Räumen entweichen kann (Fenster, Türen, Luftumwälzung). Anderer seits müssen dazu geeignete Luftfeuchtegehalte (optimal: 50-60 % rel. LF) und Raumtemperaturen (optimal: ca. 20 °C) vorliegen.
Deutliche Abweichungen hiervon führen unweigerlich zu Beeinträchtigung der Ausgleichsmassen, wie labile Zonen oder Anreicherung von Kunststoffen an der
Oberfläche (Farbänderungen, Schlieren).
Auch die Werkstoffe sollten klimatisch optimal gelagert werden. Im Sommer ist darauf zu achten, dass sich die Verlegewerkstoffe, vor allem die Spachtelmassen, nicht in der prallen Sonne oder im geschlossenen Fahrzeug aufheizen.
Durch übermäßige Hitze werden die Verlaufseigenschaften der Ware massiv beeinträchtigt und eine Glattspachtelung ist nicht mehr möglich. Derselbe Effekt entsteht bei deutlicher Abkühlung der Spachtelmasse. Die optimale Lagertemperatur beträgt 15 bis 25 °C.
Hättest du das gewusst?
Eine 2-mm-Spachtelmassenschicht enthält pro m2 rund 0,8 l Wasser. Wenn etwa die Hälfte davon verdunsten soll und der Raum insgesamt 20 m2 groß ist, gilt es immerhin 8 l zu beseitigen! Damit wird die Notwendigkeit einer guten Luftumwälzung/Belüftung bei Spachtelarbeiten deutlich.
Staubarme Spachtelmassen
Wie Untersuchungen der BG Bau aus der Vergangenheit zeigten, können beim Anmischen von Trockenmörteln, Fliesenklebern oder Spachtelmassen in Innenräumen kurzfristig relativ hohe Staubkonzentrationen auftreten. Einmal aufgewirbelt, verbleiben die feinsten Partikel stundenlang in der Luft und belasten die Atemwege.
Der Arbeits- und Gesundheitsschutz beantwortet derartige Fragen ohnehin eindeutig mit dem so genannten STOP-Prinzip. Dabei steht das „S“ für Substitution, das „T“ für technische Maßnahmen, das „O“ für organisatorische Vorkehrungen und das „P“ für den persönlichen Schutz. Die Rangfolge ist durch den Verordnungsgeber klar vorgegeben: Lässt sich ein belastendes Produkt durch ein weniger belastendes ersetzen, d. h. substituieren? In der Kategorie der Spachtelmassen ist dies zweifelsfrei der Fall.
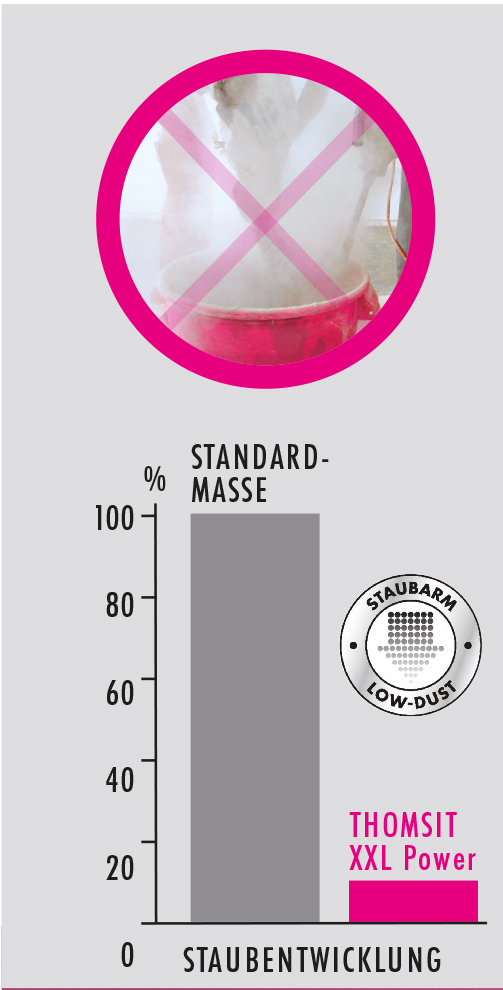
Hier setzt THOMSIT einmal mehr Akzente in puncto Arbeitsschutz und Nachhaltigkeit. So mindert z. B. die staubarm eingestellte Spachtelmasse THOMSIT XXL Power den Anteil der frei werdenden Stäube um bis zu 90 Prozent! Das gilt für den gesamten Anrührprozess – vom Ausgießen des Gebindesacks bis zum Anrühren bzw. Pumpen. So schont der Verarbeiter seine Gesundheit und erhält zugleich ein entscheidendes
Argument für die Auftragsverhandlungen an die Hand.
Denn bei Sanierungswünschen zählen Stäube und somit entstehender Dreck zu den größten Sorgen von Auftraggebern – insbesondere im privaten Bereich.
Weitergehende Informationen sind unter dem Stichwort „staubarm“ auf der BG Bau Website www.bgbau-medien.de zu erhalten.
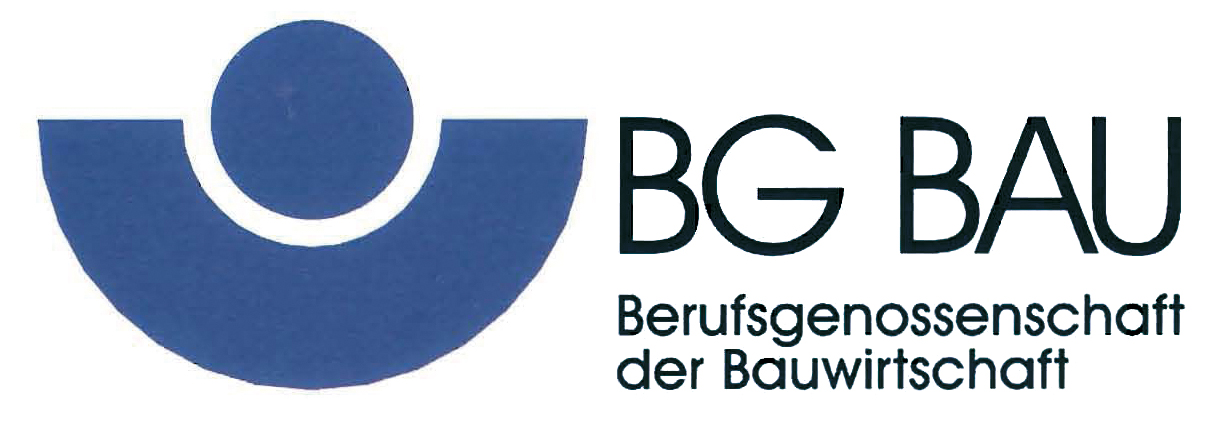
Anmischen der Spachtelmasse
Mineralische Spachtelmassen werden in dem für die jeweilige Masse angegebenen
Mischungsverhältnis mit sauberem, kalten Wasser angerührt und mit einem geeigneten Rühraggregat ca. 2-3 Min. angemischt. Deutliche Abweichungen von den herstellerseitig vorgegebenen Anmachwassermengen führen unweigerlich zu Reklamationen (schlechterer Verlauf, deutlicher Festigkeitsverlust, Oberflächenbeeinträchtigungen u. a.).
Bei Schichtdicken über 10 mm kann bei THOMSIT-Spachtelmassen, wie z. B. THOMSIT XXL Power oder THOMSIT SL 85, bis zu 30 % feuergetrockneter Quarzsand der Körnung 0-2 mm beigemischt werden.
Bei der XF 700 kann der Schichtdickenbereich von 50-70mm bei Zugabe des Quarzsands QS 20 erreicht werden. Für die XF 500 gilt dies von 20-30mm.
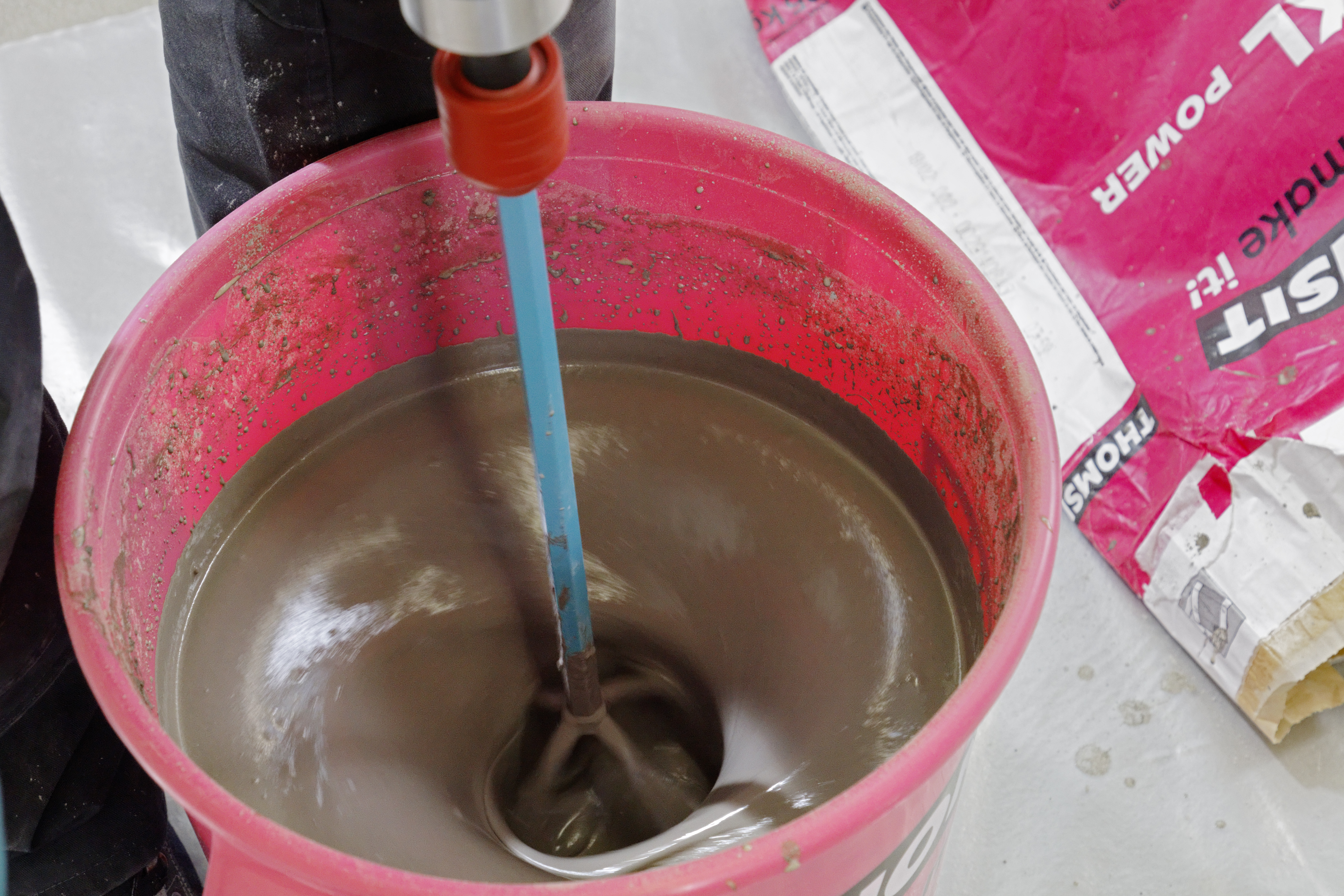
WICHTIG!
Die Zumischung von trockenem Sand erfordert kein zusätzliches Anmachwasser. Überhöhte Wassermengen führen immer zu verringerten Festigkeiten und zu verlängerten Trocknungszeiten. Selbstverlaufende Spachtelmassen reagieren bei starker Wasserüberdosierung mit Absonderung schwererer Bestandteile (Absetzen) und leichterer Feinanteile (Ausschwimmen). Damit verbunden kommt es zur Bildung einer labilen Oberflächenrandzone und einer Schwächung der Festigkeit im Gefüge.
Maschinelle Verarbeitung
Spachtelmassen lassen sich ergonomisch und schnell mittels Mörtelpumpen verarbeiten, wie z. B. duo-mix 2000 der Fa. M-Tec Mathis Technik GmbH (www.m-tec-gmbh.de). Aufgrund der Leistungsfähigkeit der einzelnen Mörtelpumpen ist es sinnvoll, sie ab einer Flächengröße von etwa 500 m2 und einer Schichtdicke von 3 mm einzusetzen. Bei kleineren Flächen (200-500 m2) macht der Pumpeneinsatz erst Sinn, wenn entsprechende Schichtdicken von deutlich über 10-15 mm eingebaut werden müssen. Weitergehende Hinweise zum Pumpen von Spachtelmassen sind bei den technischen Beratern erhältlich.
Auftragen der Spachtelmasse
Die angemischte Masse wird in der benötigten Menge auf den Untergrund gebracht und mit einem Werkzeug verteilt. Dies kann z.B. eine Glättkelle oder ein Glättschwert sein. Günstiger sind jedoch Zahnrakel, da bereits durch die Zahnung die Schichtdicke vorgegeben ist. Mit Hilfe solcher Rakel in Verbindung mit Teleskopstielen lässt sich Spachtelmasse ergonomisch auch in stehender Haltung verteilen. Grundsätzlich benötigen alle Ausgleichsmassen eine gewisse Schichtdicke, damit der Effekt des Selbstverlaufens überhaupt zustande kommt. Um hinreichend glatte Böden zu erzeugen, sind daher Schichten von mindestens 2 mm, besser 3 mm aufzutragen.
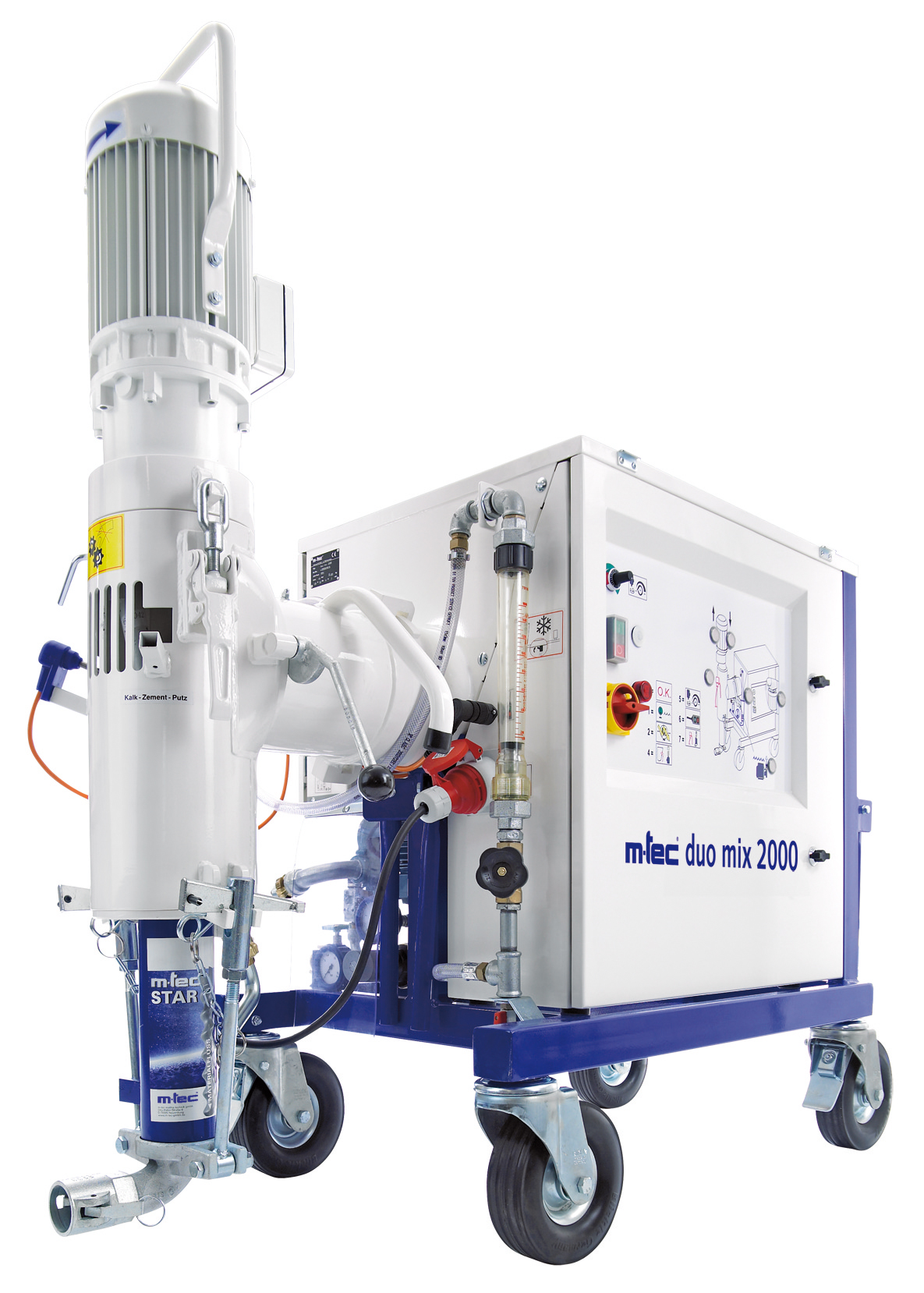
Besonders in großen Räumen sollten möglichst kurze Wege zwischen der vorangegangenen Anmischung und der weiteren eingehalten werden, um unschöne, sichtbare Übergänge zwischen diesen Bereichen zu vermeiden.
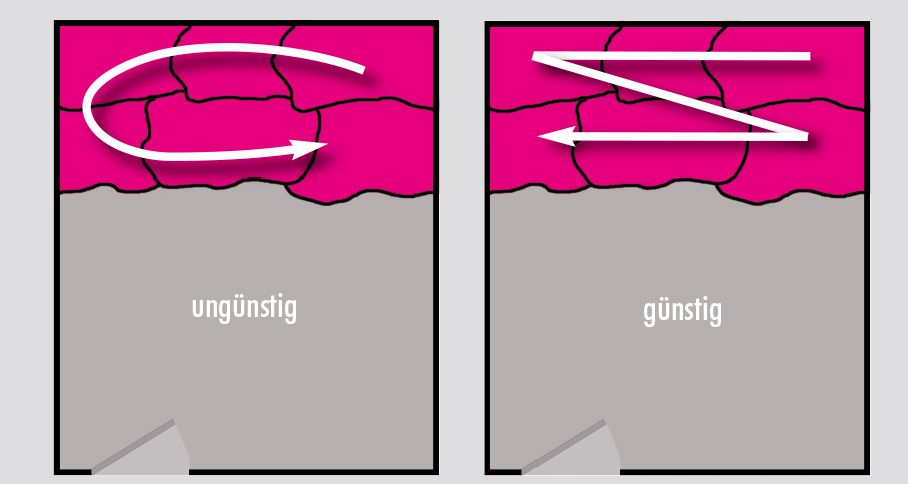
Spachteltechnik
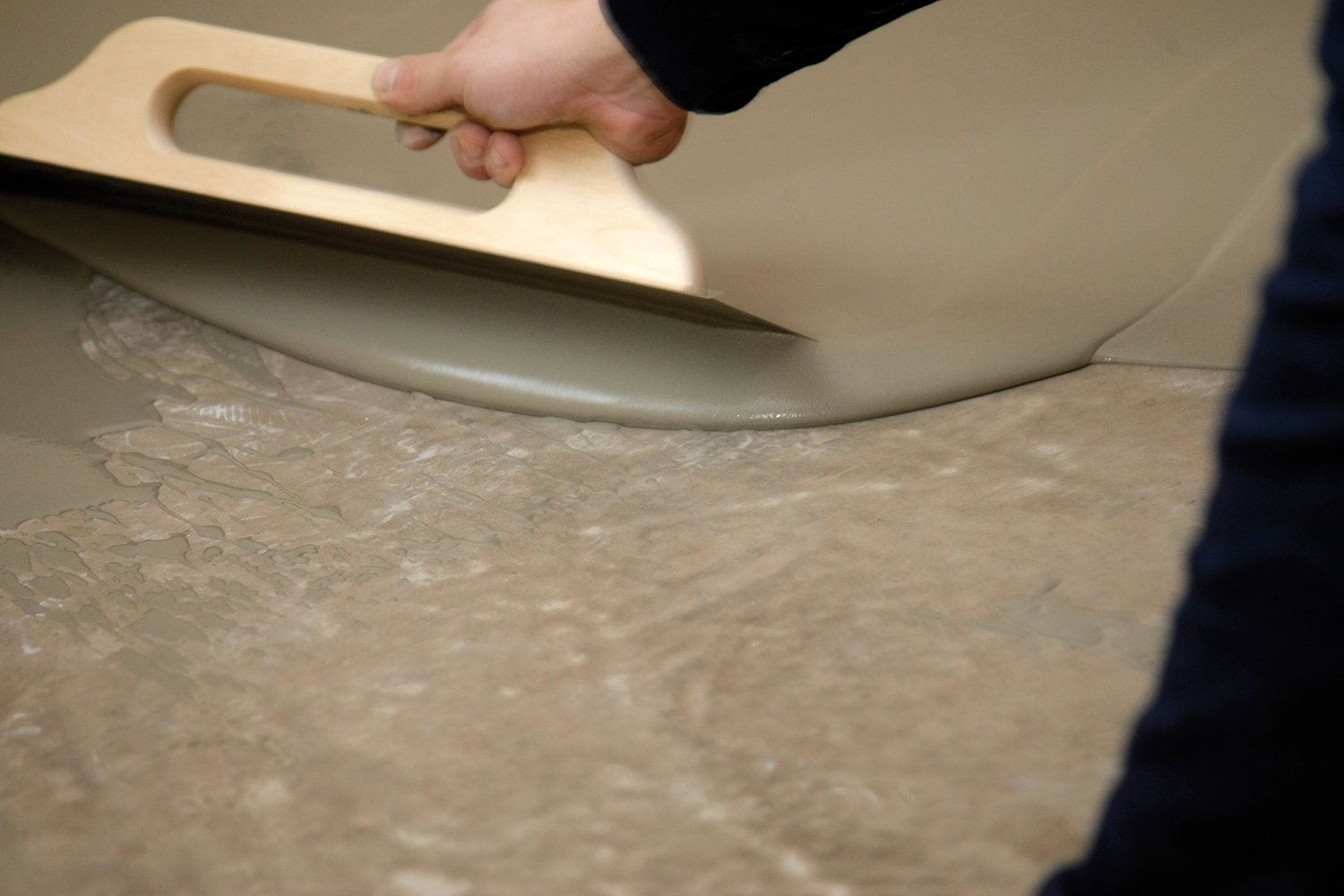
Rakeltechnik
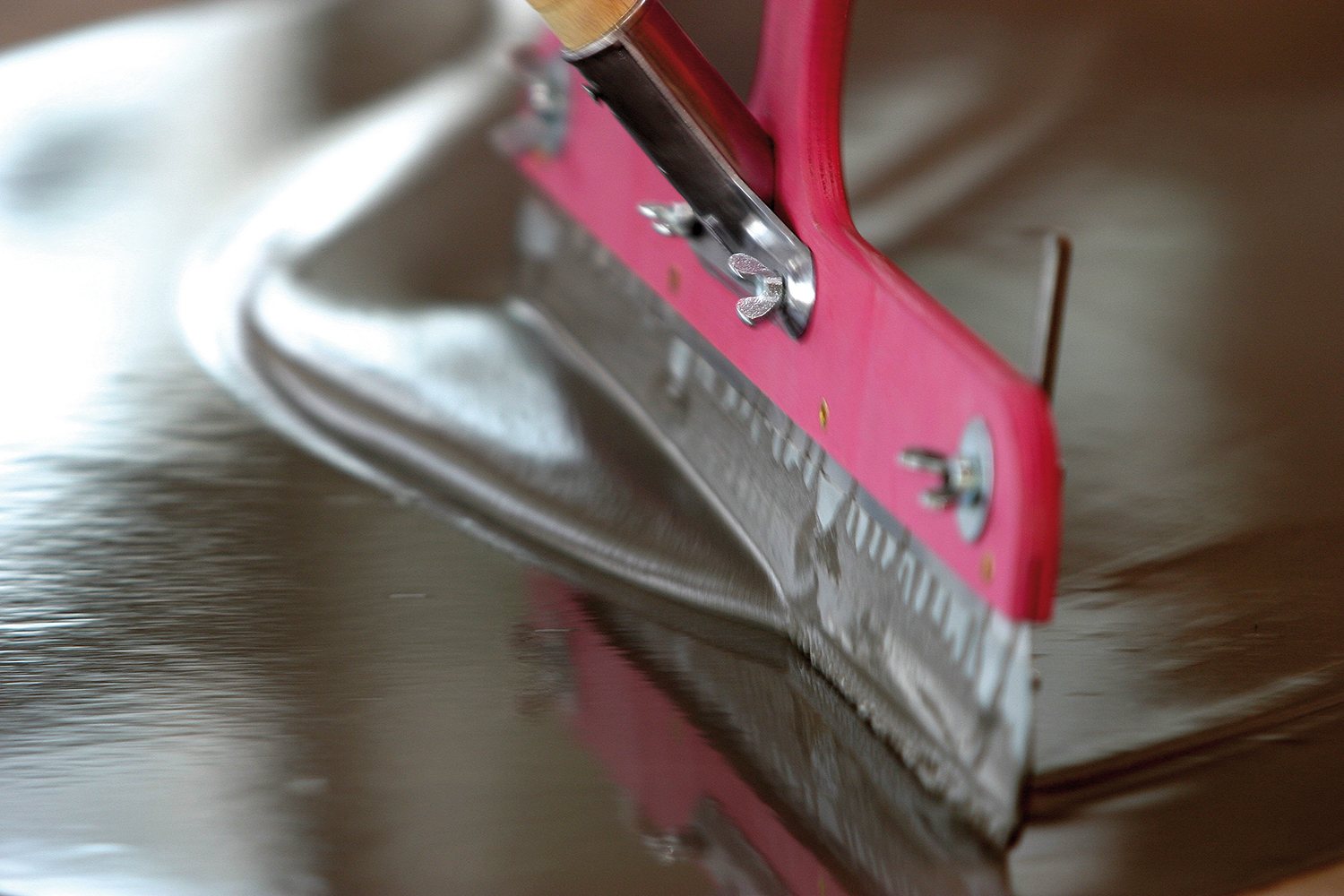
Stachelwalze
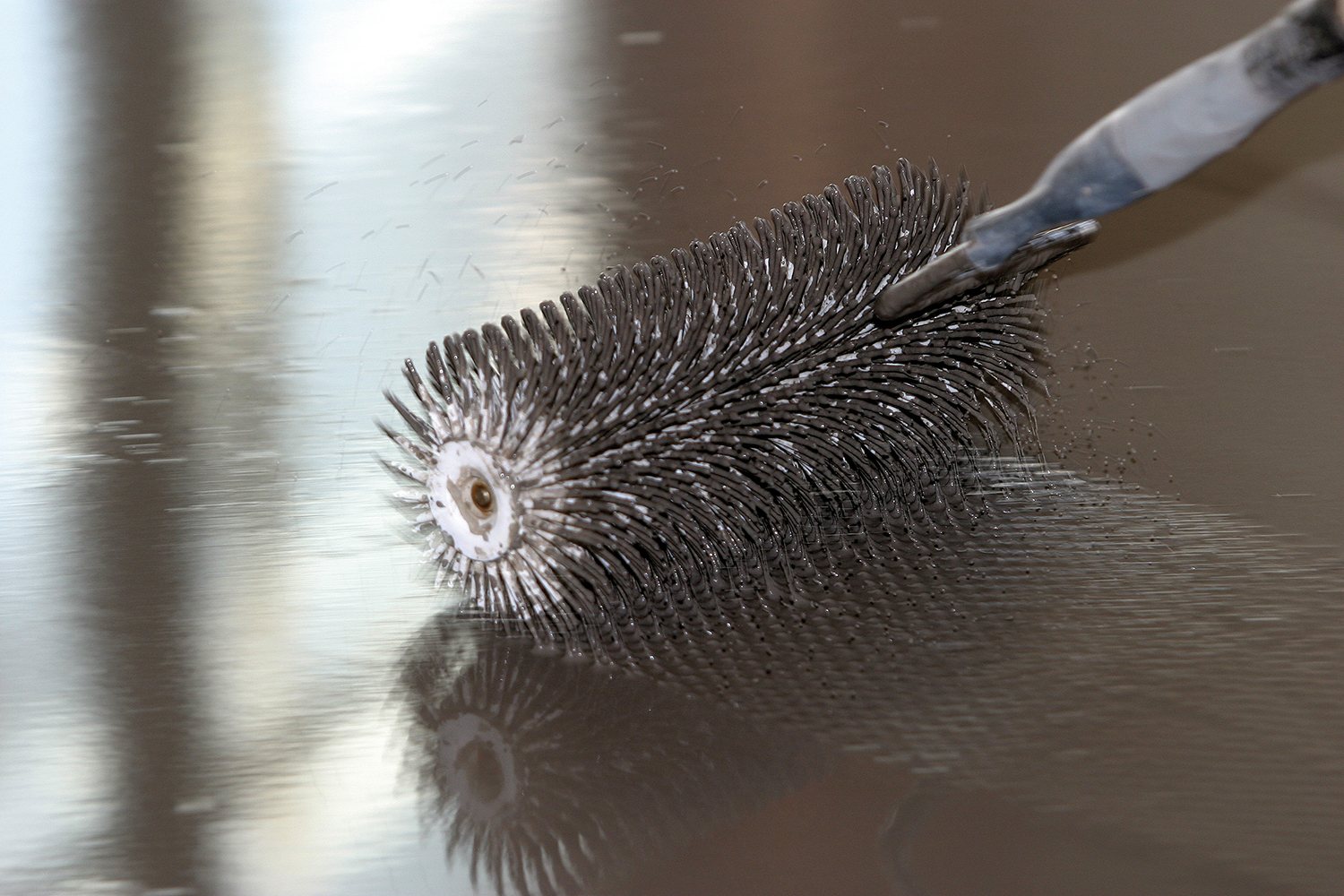
Es ist – unabhängig davon, ob manuell angerührt oder gepumpt, Rakel oder Glätter verwendet wurde – empfehlenswert, frische Spachtelflächen mit einer Stachelwalze nachzubearbeiten. Auf diese Weise werden besonders glatte, ebene Oberflächen erzielt. Zudem lassen sich Übergänge zwischen den einzelnen Anmischungen besonders gut angleichen, so dass sich später keine Abzeichnungen im Oberbelag einstellen können.
Sollte ein weiterer Ausgleichsmassenauftrag auf eine bereits gespachtelte Fläche
erforderlich sein, ist zunächst die Trocknung der ersten Schicht abzuwarten.
Die optimale Verbindung der Schichten untereinander wird mittels Zwischengrundierung mit THOMSIT R 766 Multivorstrich sichergestellt.